Power plant dusting machine anti-wear application
Power plant dusting machine anti-wear application
The equipment used in the power plant of the thermal power plant has a large amount of wear and tear, which causes many leakage points, which seriously affects the operation, environmental pollution, material waste, and frequent maintenance or renewal; especially the wind shell of powder discharge machine and the part that changes the direction of the medium flow in the pipeline, In order to extend the service life of these worn parts, the leakage is reduced, and the output of the equipment is not affected. After long-term investigation and research, we believe that the direct-adhesive wear-resistant alumina ceramic lining - the material has good wear resistance and good adhesion. Can achieve the purpose of extending equipment life, reducing leakage and improving equipment health
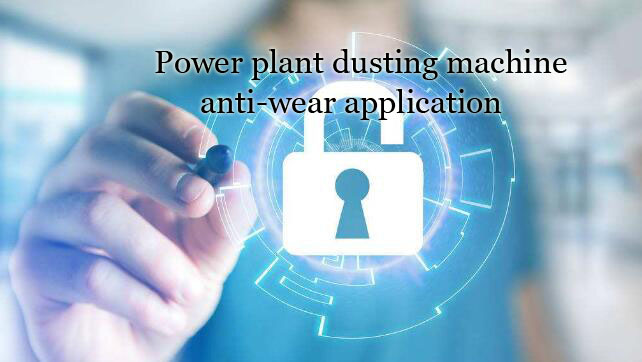
In a power plant, Each boiler unit is equipped with two powder discharge machines. The speed of the powder discharge machine is about 1450 rpm, and the medium temperature is 60-80 °C. Due to the scouring wear of pulverized coal, the service life of the powder discharge machine is low. Although various surface strengthening processes have been used, including spray welding, surfacing and coating of polymer materials, the use effect has been poor and the unit has been operated safely. One of the serious hidden dangers. At last use following measures to wear solution.
1. Surface-bonding or soldering ceramics: The wear resistant alumina ceramic lining are composited on the easy-wearing surface of the powder discharging machine by using high-strength high-temperature adhesive or special welding process. In order to ensure the service life after the anti-wear treatment, we will carry out the excavation treatment after the windshield of the powder discharge machine and the original wear-resistant ceramics of the outlet elbow, which are worn more than 1/2 of the original wall thickness and have a tendency to expand. , polish the surface to the metallic luster, then stick the wear-resistant ceramic. However, the problem of wear at the corners cannot be solved.
2. Weld a circle of 12×30 steel plate at the joint of the powder collecting machine current collector and the volute flange to prevent the airflow from passing through, reducing the shortcut, and the passing airflow can only flush the parts of the wear-resistant ceramic. This protects the volute inlet flange from wear and leakage and improves the efficiency of the powder discharge machine
As abrasion resistant alumina ceramic lining supplier, Chemshun Ceramics company solved several wear solution cases in power plant. We hope to help you more in wear protection.
The equipment used in the power plant of the thermal power plant has a large amount of wear and tear, which causes many leakage points, which seriously affects the operation, environmental pollution, material waste, and frequent maintenance or renewal; especially the wind shell of powder discharge machine and the part that changes the direction of the medium flow in the pipeline, In order to extend the service life of these worn parts, the leakage is reduced, and the output of the equipment is not affected. After long-term investigation and research, we believe that the direct-adhesive wear-resistant alumina ceramic lining - the material has good wear resistance and good adhesion. Can achieve the purpose of extending equipment life, reducing leakage and improving equipment health
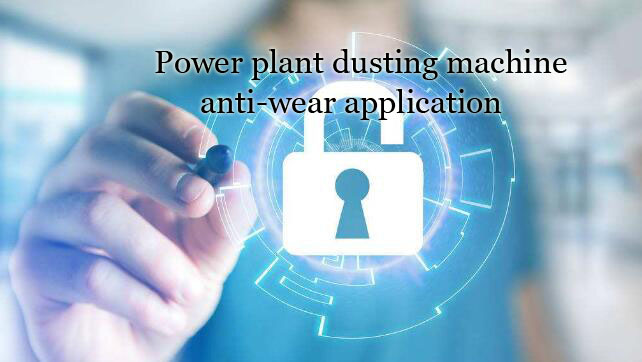
In a power plant, Each boiler unit is equipped with two powder discharge machines. The speed of the powder discharge machine is about 1450 rpm, and the medium temperature is 60-80 °C. Due to the scouring wear of pulverized coal, the service life of the powder discharge machine is low. Although various surface strengthening processes have been used, including spray welding, surfacing and coating of polymer materials, the use effect has been poor and the unit has been operated safely. One of the serious hidden dangers. At last use following measures to wear solution.
1. Surface-bonding or soldering ceramics: The wear resistant alumina ceramic lining are composited on the easy-wearing surface of the powder discharging machine by using high-strength high-temperature adhesive or special welding process. In order to ensure the service life after the anti-wear treatment, we will carry out the excavation treatment after the windshield of the powder discharge machine and the original wear-resistant ceramics of the outlet elbow, which are worn more than 1/2 of the original wall thickness and have a tendency to expand. , polish the surface to the metallic luster, then stick the wear-resistant ceramic. However, the problem of wear at the corners cannot be solved.
2. Weld a circle of 12×30 steel plate at the joint of the powder collecting machine current collector and the volute flange to prevent the airflow from passing through, reducing the shortcut, and the passing airflow can only flush the parts of the wear-resistant ceramic. This protects the volute inlet flange from wear and leakage and improves the efficiency of the powder discharge machine
As abrasion resistant alumina ceramic lining supplier, Chemshun Ceramics company solved several wear solution cases in power plant. We hope to help you more in wear protection.
评论
发表评论